SRM Industries are one of the UK's leading custom rubber moulding specialist with over 40 years experience
SRM Industries – Building a world-class custom rubber moulding facility
SRM has over 40 years experience of custom rubber moulding and are one of the leading rubber product manufacturers in the UK with an unparalleled knowledge of injection and compression rubber moulding.
The last 18 months alone has seen SRM invest in 11 new state-of-the-art Maplan injection moulding machines and 2 new Mewo cryogenic de-flashing machines, cementing SRM’s place as a front runner within the industry.
We work across a broad range of industry sectors including: electronic, rail, petrochemical, construction and medical, to name but a few. All our moulds are engineered in-house by our highly skilled toolmakers on CNC machining centres; this gives our customers the peace of mind that we can manage the whole process from initial design through to distribution on time and on budget.
Innovation is at the heart of our business; we are a forward-thinking firm. Through a combination of innovation and technical know-how, we are able to deliver time and again where others stumble. We go the extra mile to make it happen.
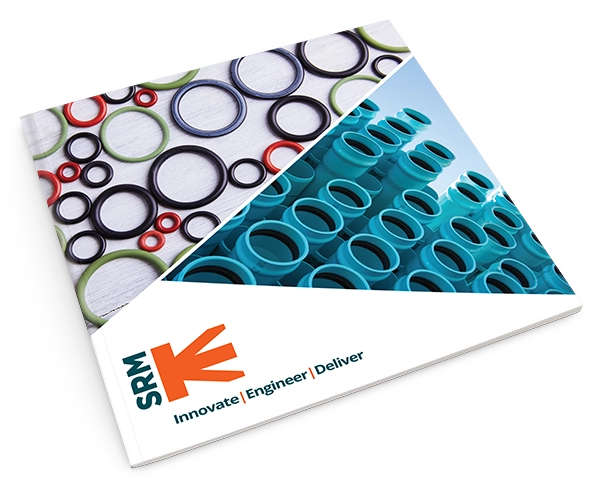
Unlocking the Potential of Custom Rubber Moulded Parts
Custom rubber moulded parts offer numerous advantages over off-the-shelf alternatives. Whether you require specific dimensions, unique shapes, or specialised materials, custom rubber moulding allows for the creation of parts that perfectly match your requirements.
One of the main advantages of custom rubber moulded parts is their ability to improve functionality. By precisely designing parts to fit your equipment or machinery, you can enhance performance and ensure optimal operation. For example, custom rubber seals can provide a watertight and airtight seal, preventing leaks and reducing energy loss.
In addition to functionality, custom rubber moulded parts can also significantly improve durability. By selecting the right materials and manufacturing processes, you can create parts that withstand harsh environments, extreme temperatures, and chemical exposure. This durability translates into reduced maintenance and replacement costs, saving you both time and money.
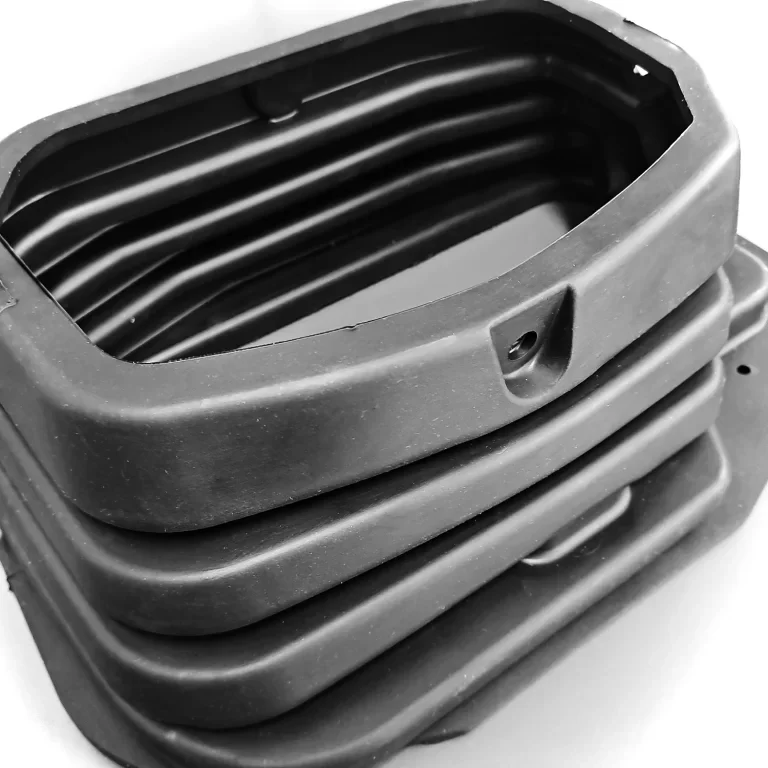