RUBBER MOULDING
Based in the heart of the UK, we are a 24-hour rubber moulding operation, offering a wide variety of moulding capability.
We offer technical design assistance at all stages, working closely with the customer from initial concept and prototyping, through tool design, production runs and aftersales.
6 types of rubber we use
There are six main rubber compounds we use depending on the requirements of the finished part ie. heat resistance, ozone resistance etc. Below is our resistance guide for the big six.
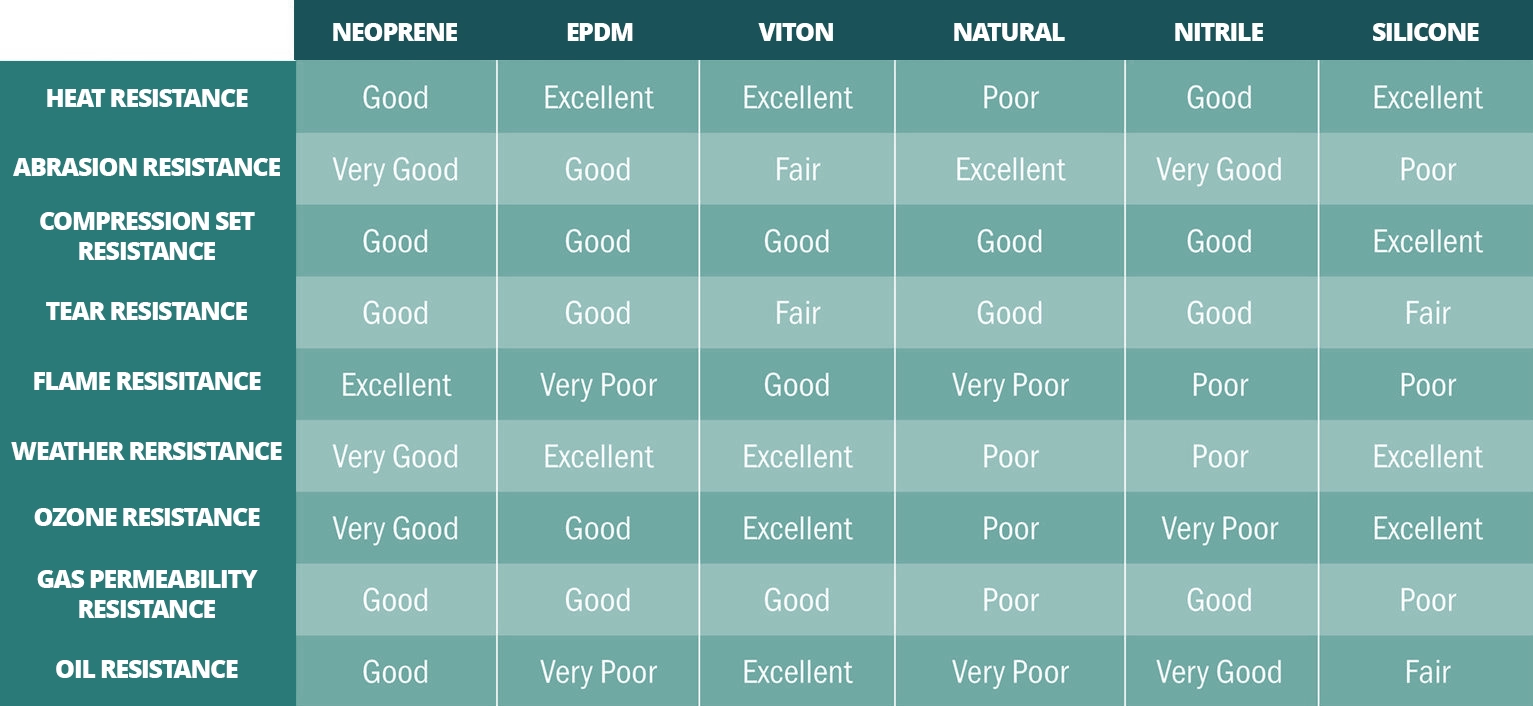
Boost Your Manufacturing Process with SRM - Experts in Rubber Moulding
Introduction to Rubber Moulding
Rubber moulding is a versatile and essential manufacturing process that has been widely adopted across various industries. This technique involves shaping and forming raw rubber materials into specific shapes and designs to create a wide range of products, from automotive parts to consumer goods. At SRM, we have refined and optimised this technology to help our clients achieve their manufacturing goals and enhance their production capabilities.
The Importance of Choosing the Right Moulding Company
In the world of manufacturing, the choice of a rubber moulding company can make all the difference in the success of your project. A reliable and experienced partner can not only ensure the quality and precision of your final products but also streamline your production process, reduce costs, and help you stay ahead of the competition. By partnering with SRM, you can be sure you are in a safe pair of hands, and through innovation we will help you stay one step ahead of your competition.
Understanding the Manufacturing Process
The rubber moulding process involves several key steps, each of which requires meticulous attention to detail and a deep understanding of the technology. At SRM, we have mastered this process, from the initial material selection to the final product inspection. Our team of skilled professionals can guide you through every stage, ensuring that your project is executed with the utmost precision and efficiency.
- Material Selection: We carefully select the most suitable rubber compounds based on your specific requirements, taking into account factors such as durability, flexibility and environmental factors such as ozone resistance, resistance to temperature fluctuations and chemical resistance.
- Tool Design: Our in-house engineering team collaborates with you to design the perfect tool that will shape your rubber components, ensuring a seamless fit and optimal performance.
- Moulding Process: Using state-of-the-art equipment and advanced techniques, we meticulously manufacture your rubber parts, maintaining strict quality control measures throughout the process.
- Finishing Touches: After the moulding process, we apply any necessary finishing, such as post curing, hand and cryogenic freeze trimming and ultrasonic cleaning ensure that your products meet the highest standards of quality and appearance.

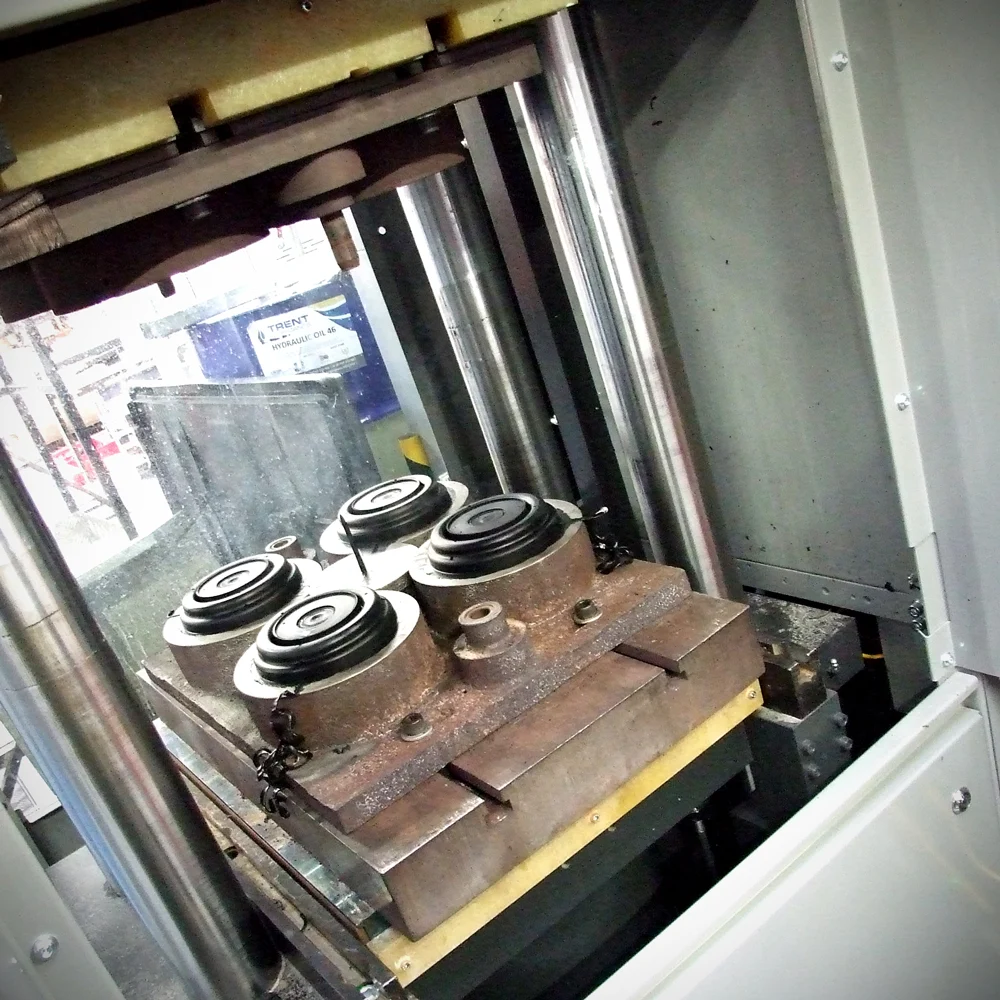
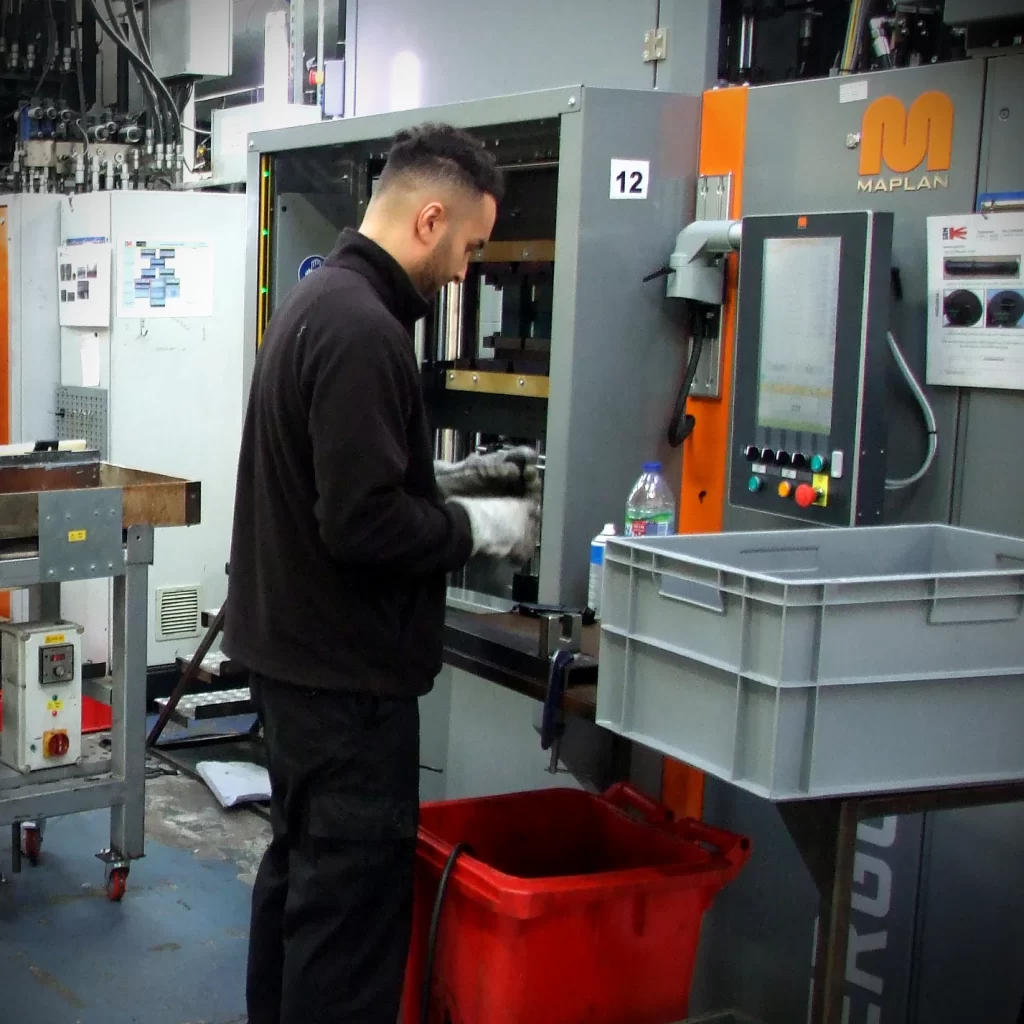
Benefits of Working with SRM – Experts in Rubber Moulding
Partnering with SRM offers a wealth of benefits that can transform your manufacturing operations. Here are just a few of the advantages you can expect:
- Improved Product Quality: Our commitment to excellence and attention to detail ensure that your rubber components are consistently produced to the highest standards, ensuring the reliability and longevity of your products.
- Enhanced Efficiency: By streamlining your manufacturing process and leveraging our expertise, we can help you increase productivity, reduce lead times, and optimise your overall operations.
- Cost Savings: Through our efficient processes, strategic sourcing, and economies of scale, we can help you achieve significant cost savings, allowing you to remain competitive in the market.
- Customised Solutions: Our team works closely with you to understand your unique requirements and develop tailored solutions that perfectly fit your needs, whether it's a small-scale project or a large-scale production run.
- Ongoing Support: We don't just deliver your products and move on; we provide ongoing technical support, troubleshooting, and collaborative problem-solving to ensure the continued success of your manufacturing endeavours.
Factors to Consider When Selecting a Moulding Company
Choosing the right rubber moulding company is a critical decision that can have far-reaching implications for your business. When evaluating potential partners, it's essential to consider the following factors:
- Industry Experience: Look for a company with a proven track record of success in your specific industry, as they will have a deeper understanding of your unique requirements and challenges.
- Technological Capabilities: Ensure that the company has access to the latest equipment, tools, and manufacturing techniques to deliver high-quality products and innovative solutions.
- Quality Assurance: Examine the company's quality control processes, certifications, and commitment to continuous improvement to ensure that your products meet the highest standards.
- Flexibility and Responsiveness: Choose a partner that is agile, adaptable, and responsive to your changing needs, allowing you to pivot and adapt to market demands.
- Customer Service: Prioritise a company that values customer satisfaction and provides exceptional support throughout the project lifecycle, from initial consultation to post-production assistance.
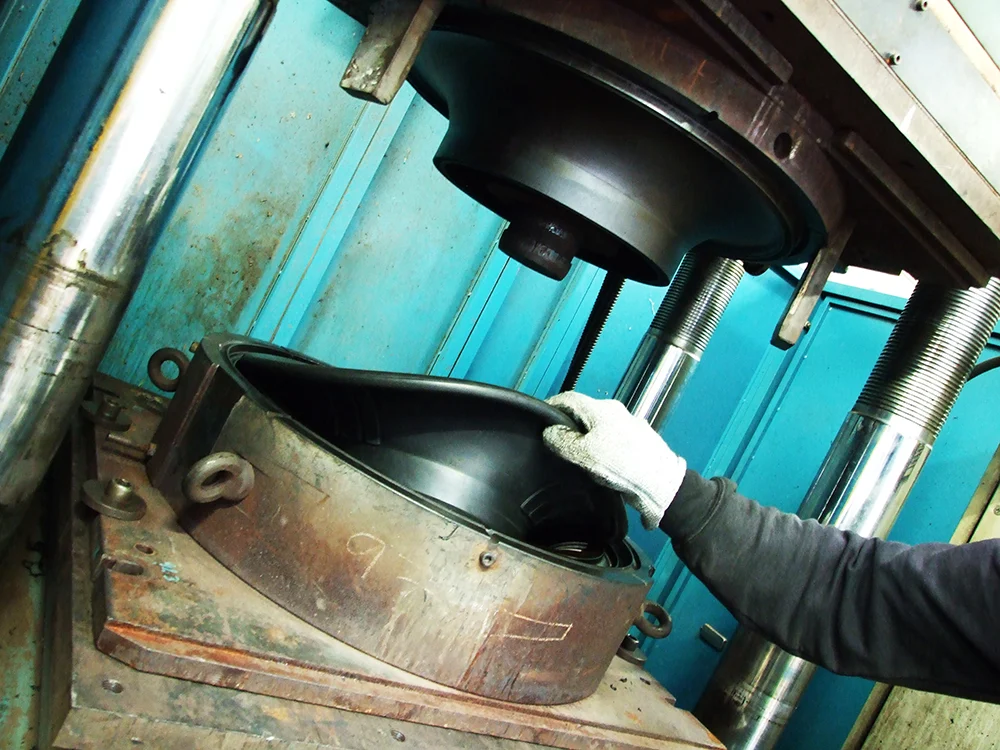
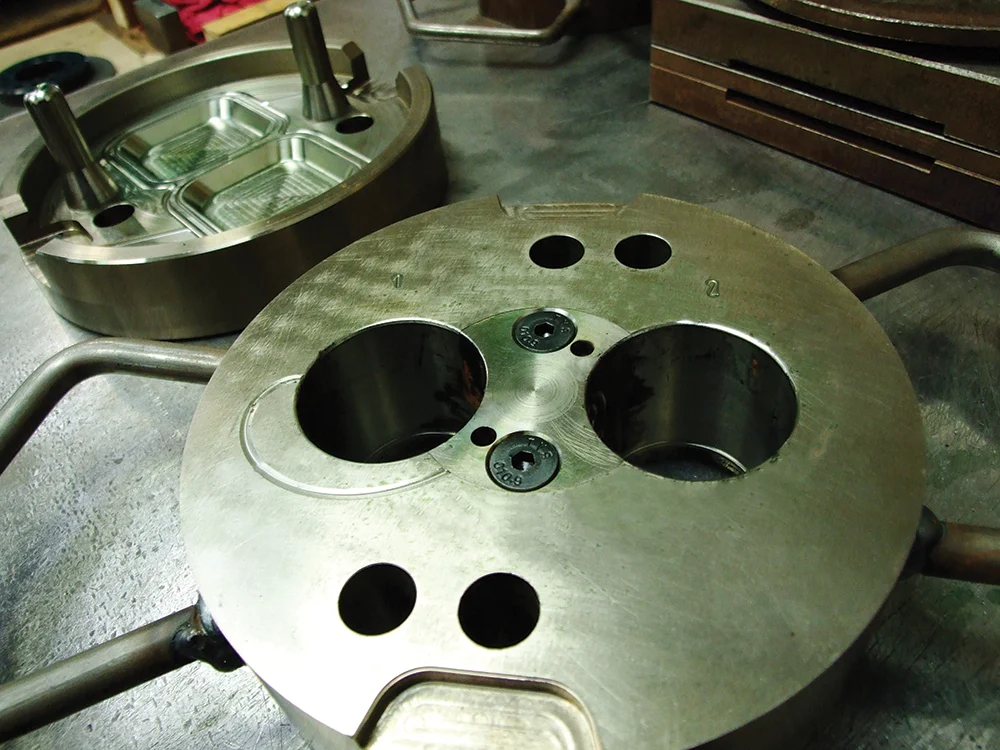
Services Offered by a Reputable Moulding Company
At SRM, we pride ourselves on offering a comprehensive suite of services to meet the diverse needs of our clients. From initial design and prototyping to large-scale production and post-manufacturing support, we have the capabilities to handle every aspect of your rubber moulding requirements.
Some of the key services we provide include:
- Custom Tool Design: Our in-house engineering team collaborates with you to design and fabricate custom moulds that perfectly capture your product specifications.
- Material Selection and Compounding: We carefully select the most suitable rubber compounds, considering factors such as durability, flexibility, and chemical resistance, to ensure the optimal performance of your products.
- Injection, Compression, and Transfer Moulding: Our state-of-the-art manufacturing facilities are equipped with the latest moulding technologies to produce high-quality rubber components with precision and efficiency.
- Finishing and Assembly: We offer a range of finishing services, including Freeze trimming, ultrasonic cleaning, IP testing, and assembly, to deliver a complete, ready-to-use product.
- Quality Assurance and Testing: Our comprehensive quality control measures, including rigorous inspections, testing and contactless measuring ensure that your rubber parts meet the highest standards of quality and performance.
- Prototyping: We understand the importance of agility in today's fast-paced market, which is why we offer prototyping services to help you quickly and cost effectively validate your designs and accelerate your time to market.
- Inventory Management and Logistics: To streamline your supply chain, we provide inventory management and logistics support, ensuring the timely delivery of your rubber components.
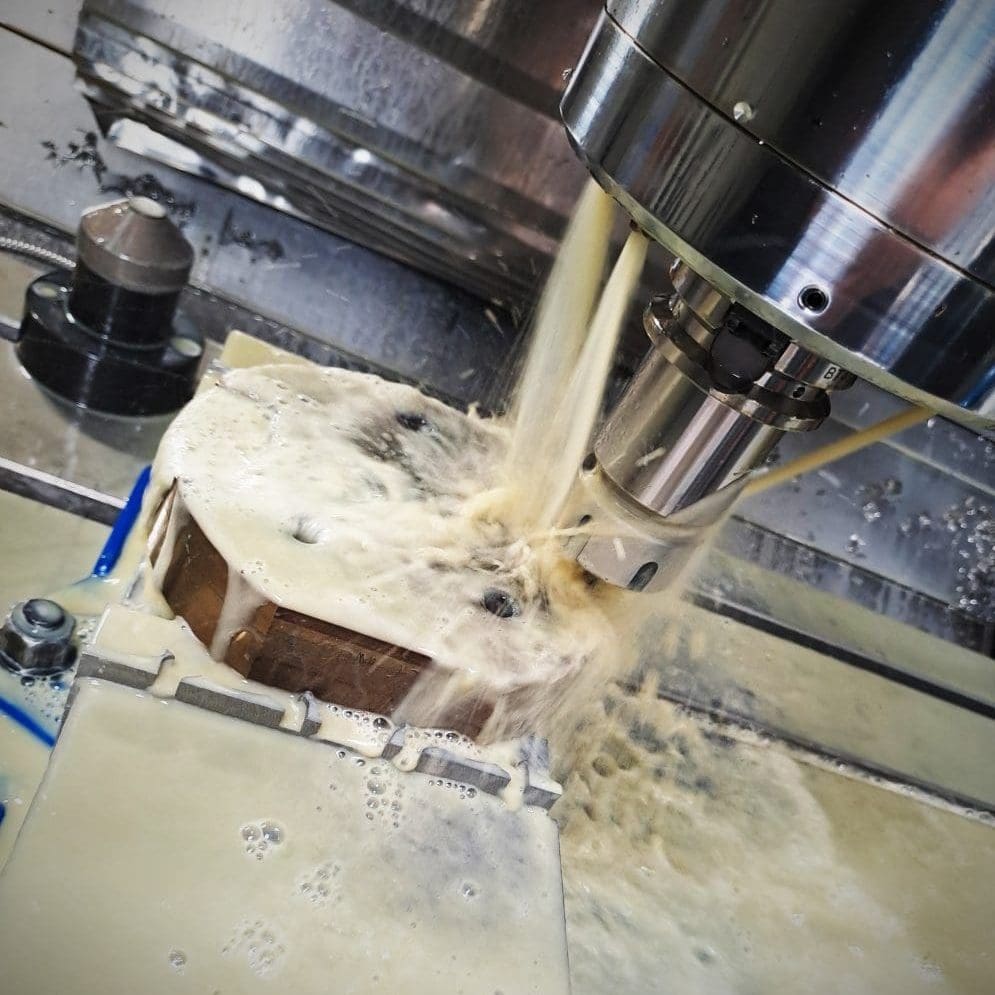
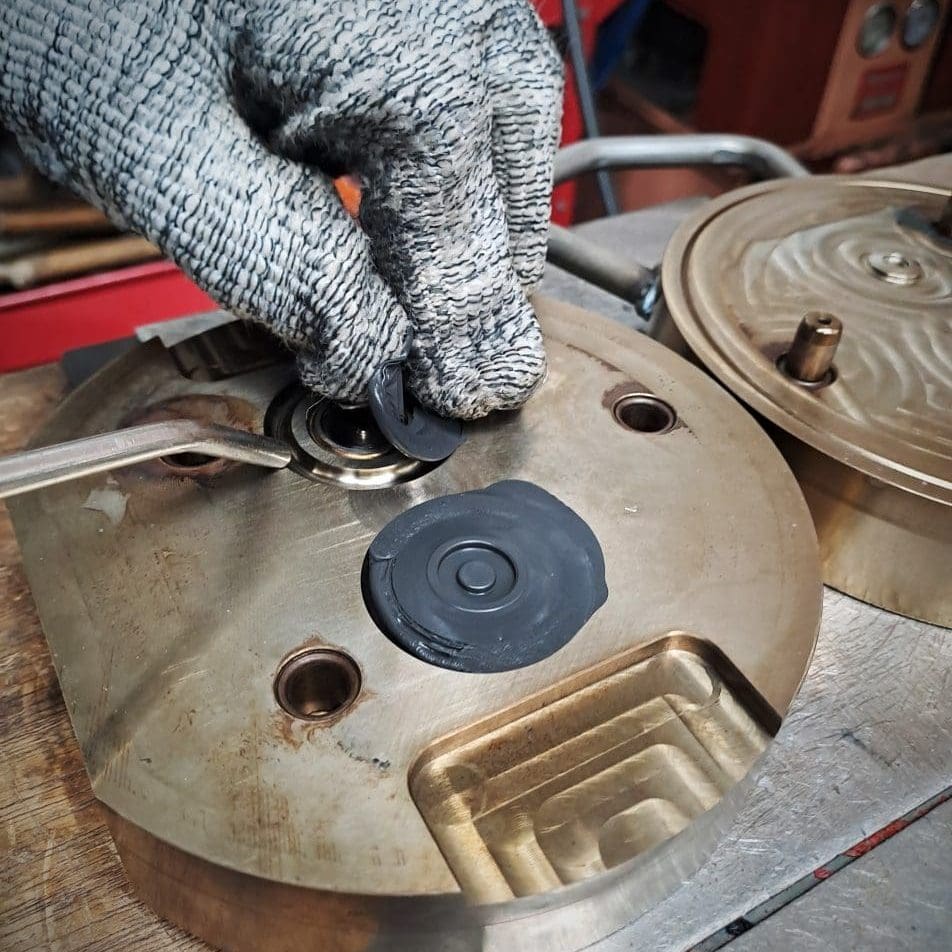
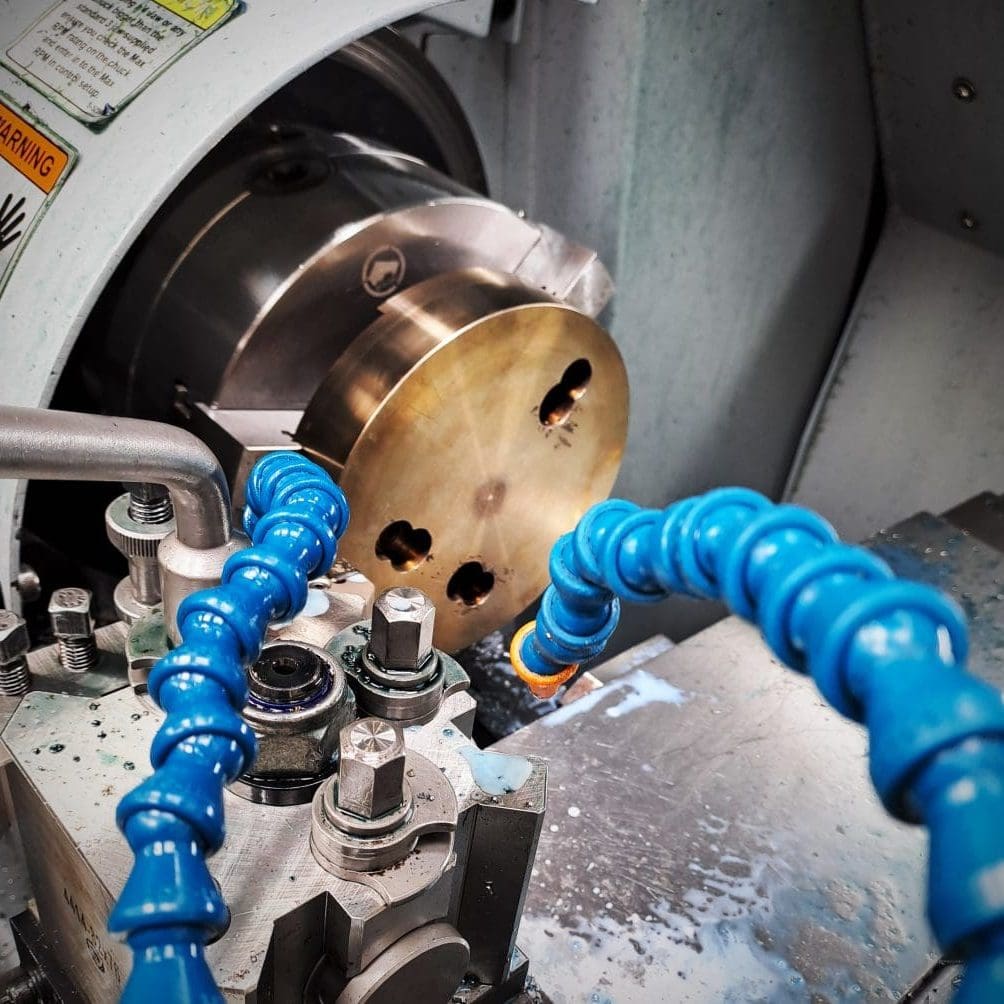
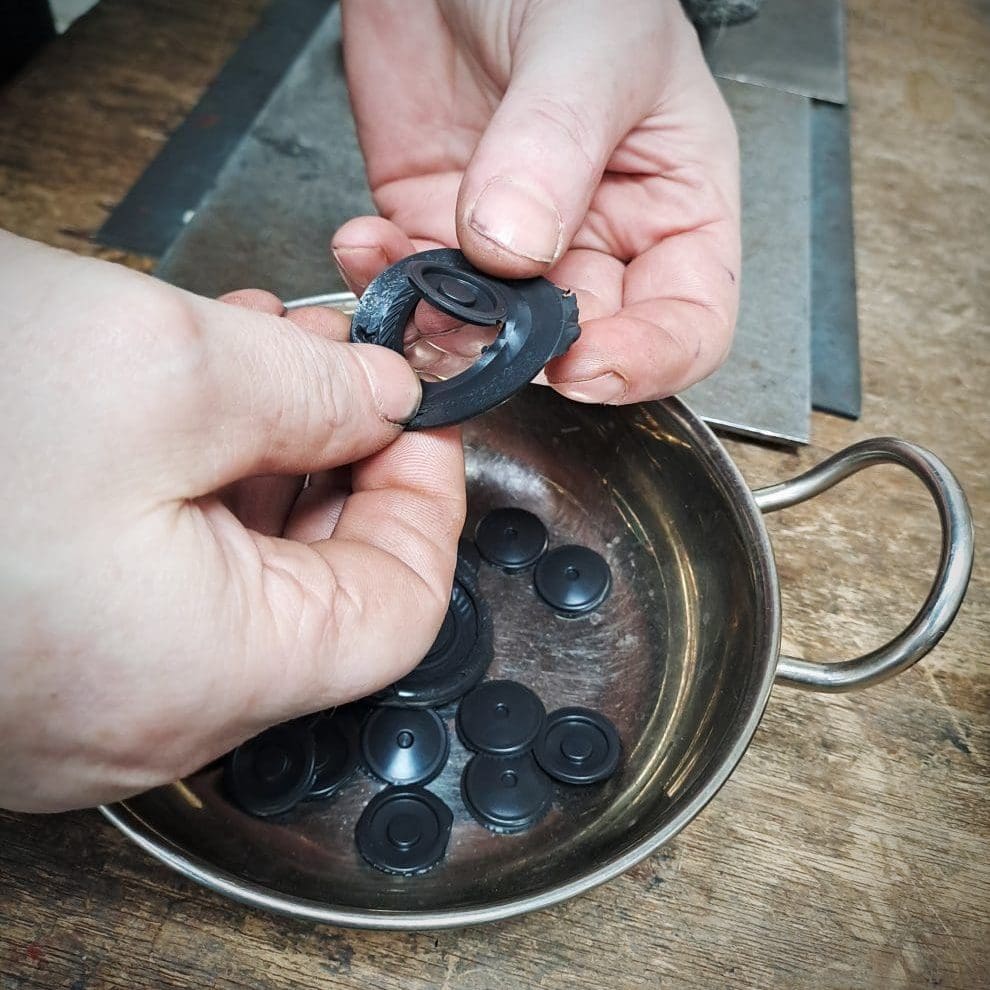
Conclusion: Why SRM is the Best Choice for Your Manufacturing Needs
At SRM, we are committed to transforming the way you approach your manufacturing processes. With our deep industry expertise, state-of-the-art facilities, and unwavering dedication to quality, we are uniquely positioned to help you unlock new levels of efficiency, cost-savings, and product innovation.
Whether you're looking to enhance the performance of your existing products or develop entirely new rubber components, our team is here to support you every step of the way. Contact us today to learn more about our comprehensive range of services and how we can help you take your manufacturing to the next level.


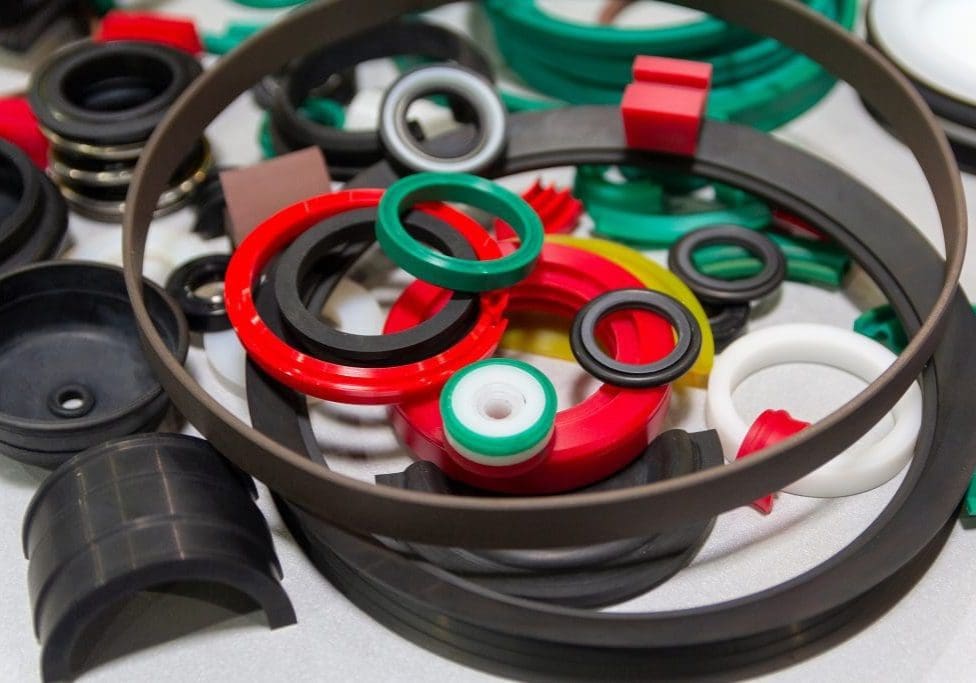

Advantages of Rubber Moulding in the UK
Rubber moulding offers numerous advantages that have contributed to its widespread adoption across various industries in the UK. Firstly, it allows for the production of complex shapes and intricate designs that would be difficult or impossible to achieve with other materials. Rubber moulding also provides excellent durability, flexibility, and resistance to chemicals, making it ideal for applications where these properties are essential. Additionally, rubber moulding enables cost-effective mass production, reducing production time and costs. The versatility and reliability of rubber moulding have made it a preferred choice for industries such as automotive, aerospace, healthcare, and consumer goods.
Finding a Reliable Rubber Moulding Company in the UK
When it comes to rubber moulding projects, finding a reliable and experienced company such as SRM is essential for successful outcomes. A reputable rubber moulding company should have a strong track record, state-of-the-art facilities, advanced machinery, and a skilled workforce. It is crucial to conduct thorough research, read customer reviews before finalising a partnership. Additionally, considering factors such as certifications, quality control processes, and adherence to industry standards will ensure the chosen company is capable of delivering high-quality rubber moulded products.