Rubber transfer moulding
What is Rubber transfer moulding
Rubber transfer moulding requires rubber compound to be cut to the size required. Transfer moulding differs from compression moulding in that the rubber is not put into the cavity of the mould and then compressed, but is compressed and then injected into the mould.
The Transfer Moulding Process
- The weighed rubber compound is placed into a portion of the mould.
- The mould is closed up and under hydraulic pressure, the rubber is forced through a small hole into the cavity. The mould remains closed until the rubber has cured.
- The plunger is raised up and the transfer pad material is removed.
- The mould is opened and the part can be removed. Any flash is hand-trimmed or removed in our cryogenic de-flashing department.
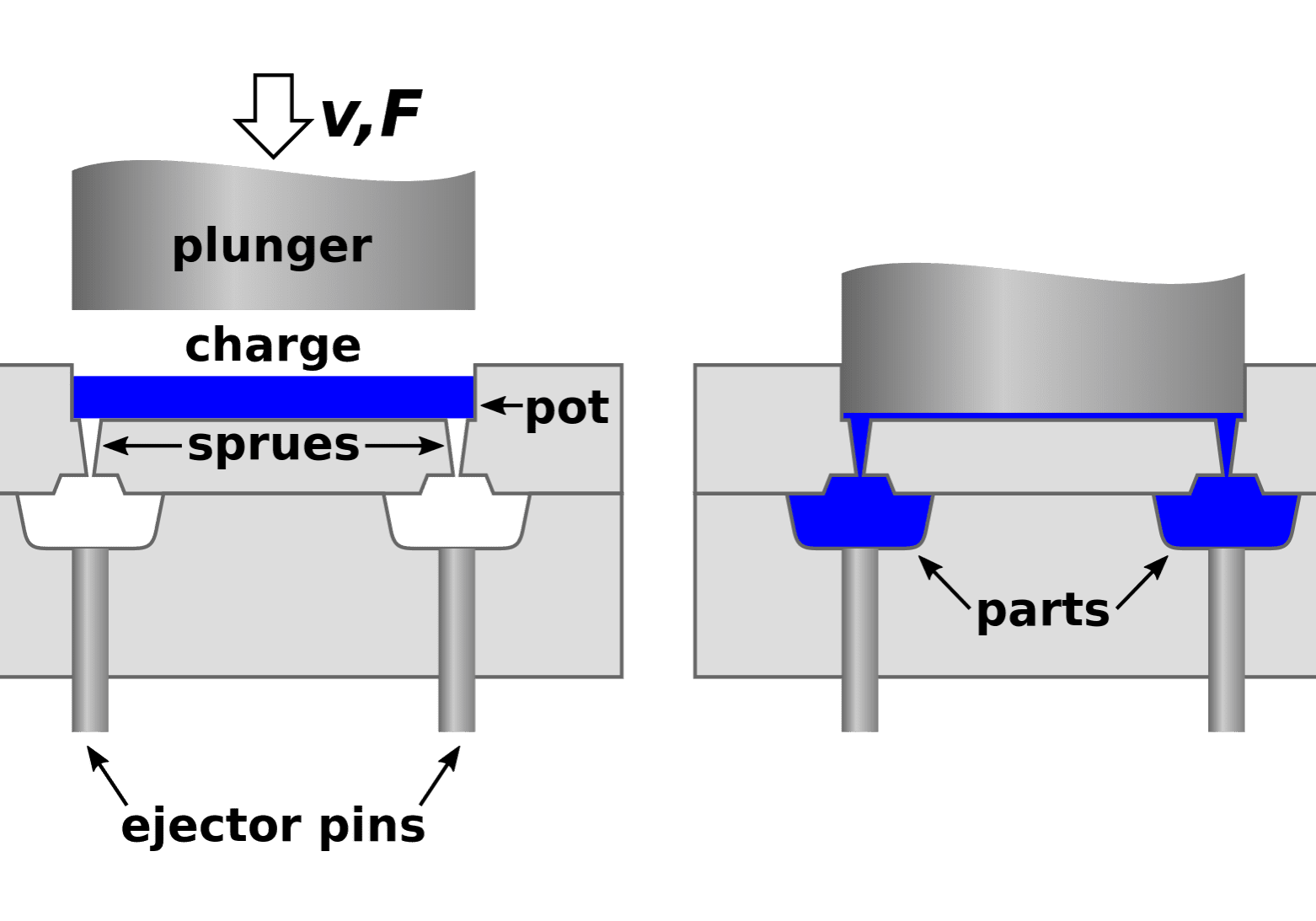
What is it used for?
Transfer moulding is a great way to create composite seals with insert mouldings which “float” in the cavity. Since cavities are independent of one another, they can move freely rather than being cut directly into the same plate. This helps to absorb variations in tolerances, so the mould will stay consistent.
Various inserts like plastic and metal can be used to make the composite seal. These allow for a bonded sealing solution, removing the need for post-assembly and providing a reliable seal.
At SRM we use the transfer moulding process for short run applications that are not suitable for compression moulding. For longer runs we would always favour injection moulding as this gives greater consistency across large batches and is ultimately more cost-effective for our clients.
A typical example where we would use transfer moulding would be for the electronic industry, where we produce DIN plugs.
Any type of rubber can be used in the transfer moulding process; this is driven by the end usage and environmental demands put on it: from UV and ozone to extreme temperatures. Whatever the application we have the perfect rubber compound to suit.

The Advantages of Transfer Moulding
- Greater uniformity - dimensionally consistent across a production run
- Tight control of dimensional tolerances - the process allows for tighter tolerances and more intricate parts.
- High cavity count - this is an advantage over compression moulding, and can save a significant amount of time in the moulding process.
- Design flexibility - transfer moulding allows for sharper edges.
- Less flash - reduces de-flashing times.
- Short production cycle - transfer moulding offers shorter cycle times than compression moulding.
- Reduced tooling lead times – shorter lead times than injection moulding.
The Disadvantages
- Complex moulds - since the design and mould tends to be complex, tooling can also become expensive compared to compression moulding
- Waste material - transfer pots typically produce higher volume waste than traditional overflows in compression tools.
- More maintenance - inserted transfer tools require more mould maintenance than compression tools.
- Slow cycling - slower production cycle than an injection tool.
Overall, the process of transfer moulding is ideal when looking to form parts which require exact positioning of bonded inserts, complex parts with lower volume requirements or multi-cavity mould designs.
Although more expensive than compression moulding, transfer moulding offers shorter production cycle times with greater batch quantities. It bridges the gap between the low-cost tooling of compression moulding and the larger upfront tooling costs of injection moulding and therefore lends itself to short run jobs that are too complex for compression moulding and too cost-prohibitive for injection moulding.
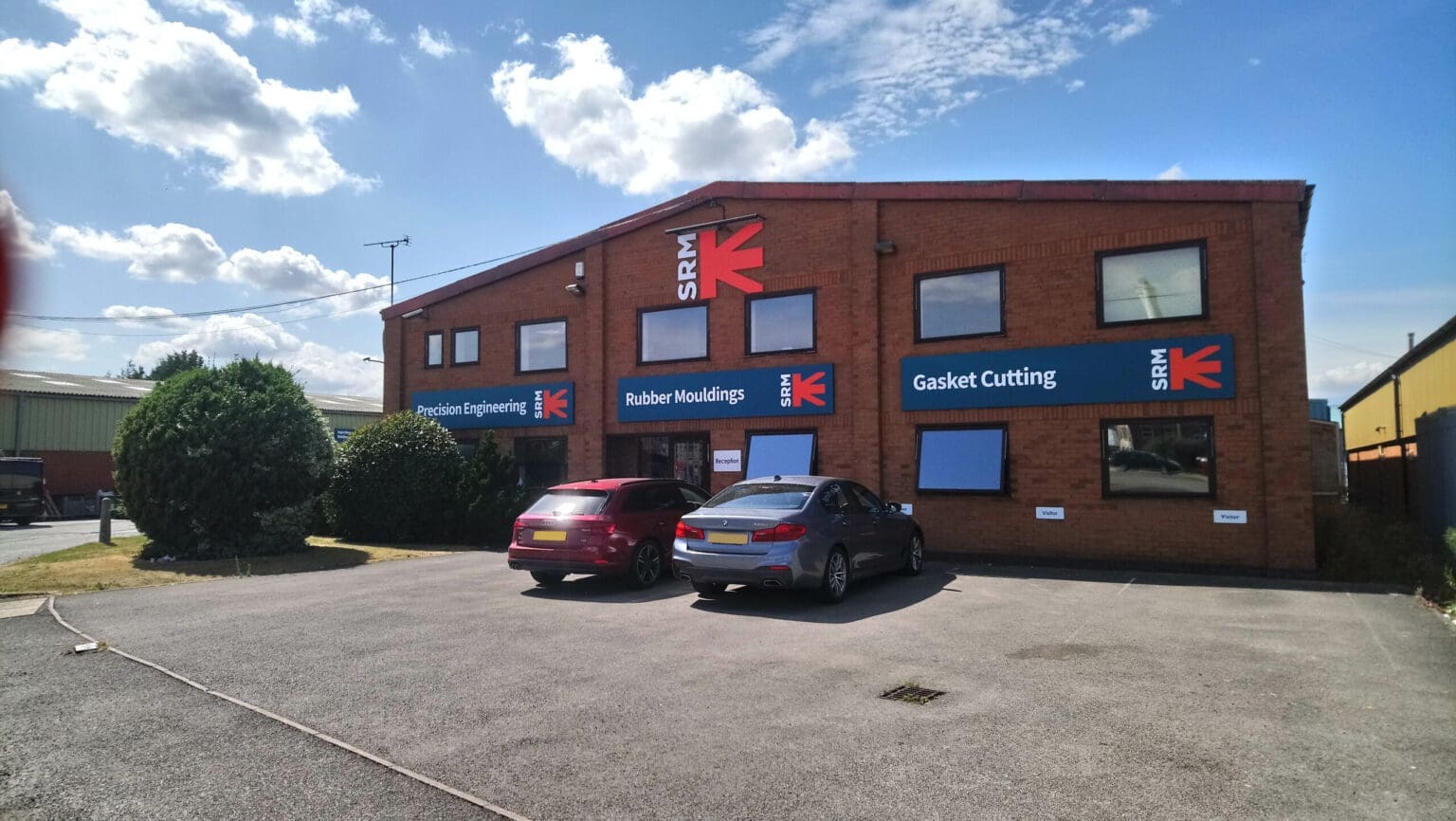
Why Use SRM for Rubber Transfer Moulding
Here at SRM we’ve been producing transfer moulded products and components for over 40 years and have an extensive knowledge of its properties and applications. We have lab facilities where we have developed our own compounds for optimum performance every time.
We hold a broad range of stock materials and can produce all tooling in-house. Because of this, we have no minimum quantity and can produce anything from one-offs to one million.
For more information or to discuss your requirements, email sales@srm-industries.com